MIM注射成型零件的设计理念
粉末冶金中注射成型技术更能够满足市场发展的需要,MIM厂家也应时而起,在2021年东睦集团投资巨资打造连云港东睦新材料有限公司MIM注射成形生产厂房,形成常规粉末冶金压制和MIM技术双腿行走,成为东睦集团最大的生产基地之一。在结构上面,注射成型能够满足设计者更多的设计灵感,因为MIM零件的设计可以跟塑料注射成形一样,不受传统的金属成形工艺影响,从中省去很多机加工,对于复杂的零部件、一些有重量要求、原材料昂贵、多个零件合成一个组合件等的特殊要求的零部件特别合适。
连云港东睦新材料有限公司接受很多新产品开发,这些新产品很多都是铸件或者工业塑料尼龙件改成常规粉末冶金工艺或是MIM注射成形工艺。价格都会很大的优势,在现代社会信息透明化,利润透明化的时代,成本对于一家实体来说,至关重要,决定市场竞争力度。
下面是连云港东睦新材料有限公司在设计注射成型件需要考虑的细节问题。
1.注射成型件厚度不同该如何过滤?
很多零部件的壁厚设计不是一样的厚度,在不同厚度转换之间应该要有过渡段,不能突然增大或是减少,应当缓缓的增或减。但是如果可以的话,最好使注射成型件的壁厚一致,因为壁厚不同回导致扭曲,开裂等原因,另外注射成形烧结会产生收缩,壁厚不易把握,会影响零件的尺寸和公差。
2.脱模斜度
脱模斜度是表面上的小角度,要平行与模型零件的移动方向,对于芯杆要求特别精确。脱模斜度是为了便于脱出与顶出成形的零件坯件。脱模斜度为0.5-2度。实际上脱模的角度根据注射成形件的复杂程度增大。
3.倒角与倒圆
倒角和倒圆可减小结构特征交会处的应力;消除了可能会到导致模型结构开裂腐蚀的尖角,便于注射料流入模型中和有助于零件从型腔中脱出,有利于成形作业的进行。
4.螺纹、孔、槽
注射成形可以直接做出内、外螺纹,孔和槽,但是在模型成本的开销会增加。
5.灌浇口
MIM注射成形件需要将注射料通过灌浇口冲去模型当中,这些浇口一般都比塑料成形要大的多,所以每一个MIM注射成型件都的很清楚,后期需要单独处理一下浇口,可以将浇口设计成凹面,也可以做磨平处理。MIM注射成型可以实现多腔模型一起注射,所以浇口的大小后期要调整一下,一般浇口会设计在注射成形件最厚的壁面上。
6.分型线
最好所有注射成型件的分型线与零件是垂直,这样方面零件从模型中取出,常常将分型线变成零件表面的征示线,这是两个对半模型拼合的必然结果。若果注射成形件的结构只在上一半,下半面没有结构,那么分型线可以在零部件的底部隐藏起来。
7.LOGO图样
很多公司在于粉末冶金厂家合作,需要在粉末冶金产品上打上公司名称,应当提前选择零部件适当的表面。
8.烧结过程
粉末冶金厂家对于烧结炉的气氛要求严格,所有粉末冶金产品在烧结过后都会有缩小的变化,这一点注射成形比粉末冶金压制要缩的比例大的多,一般在20%左右,也就是注射成形零部件毛坯很大,烧出来就缩很小。为了减少这样的形变产生的扭曲变形降到的最低限度。必须对注射成形件做支撑。
9.不可完成的尺寸处理
注射成型件在烧结到最终尺寸公差在0.3-0.5之间,如果说一个零部件某一个结构特征公差要求比较紧密,可以通过后续的机加工来完成。MIM注射成型做毛坯,来减少机加工费用,注射成形材料可以进行切削、螺纹、钻孔、精整、磨削、焊接、热处理等等工艺。
总结:在连云港东睦有常规粉末冶金和注射成形两种技术,如图所示:
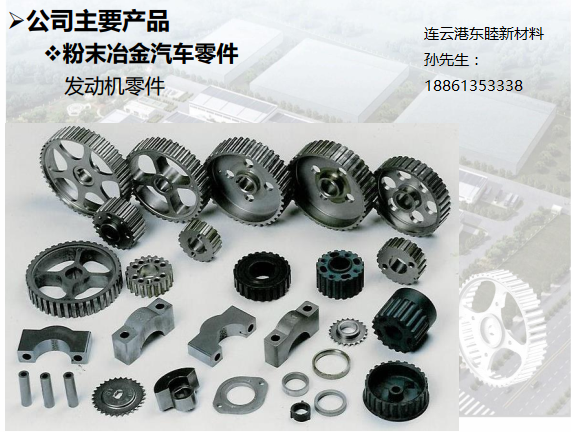
图1为粉末冶金产品
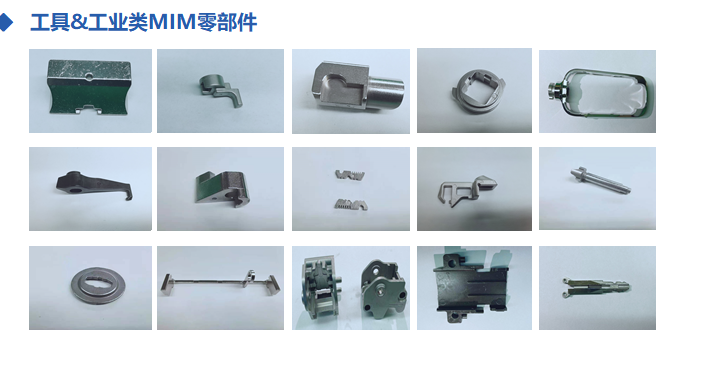
图2为MIM产品
从产品的外观上,我们可清楚看到MIM零件复杂程度比粉末冶金PM要更大一点,所以在设计之初考虑的工艺也要更多一点,比如:壁厚均一、厚度过渡段、脱模斜角、倒角倒圆、分型线、烧结后的收缩、后续机加工、灌浇口等问题。目前粉末冶金运用的领域非常广,仍然需要粉末冶金厂家不断拓展和攻克更多新型技术。在东睦集团粉末冶金厂家设有粉末冶金博士后研究所,在技术方面去年投资8%营业额,约2.8亿元的研究资金,截至2019年6月30日,东睦共拥有国家发明专利76项,实用新型专利200项,软件著作权1项,外观设计专利4项,这些支持东睦粉末冶金厂家的未来,过硬的技术满足客户需要,研发和生产不同粉末冶金零部件。